Sustainable Child-Resistant Pharmaceutical Packaging for Drug Delivery
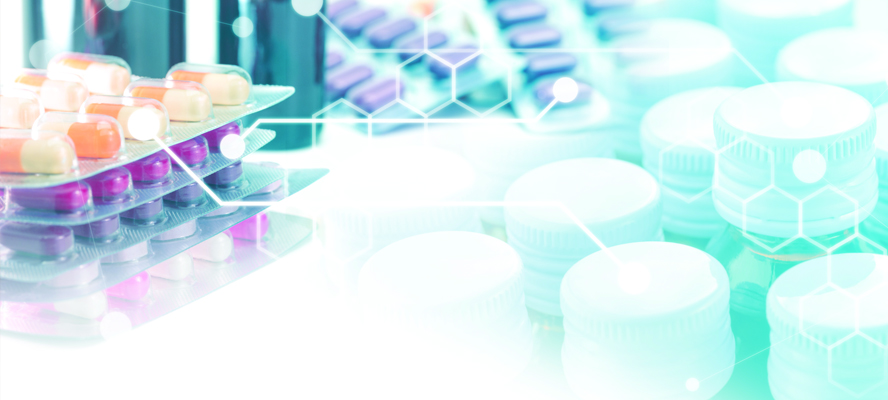
“Poisonings are frequently caused by by-products such as pharmaceuticals and home chemicals. According to the World Health Organization, child-resistant packaging has a high success rate in preventing unintentional poisoning in children. Medicines, in particular, are the leading cause of non-fatal poisoning in middle and high-income countries. As a result, specially designed packaging is a must.”
Pharmaceutical packaging has unique responsibilities in terms of its purpose. All packaging must perform several roles, such as protection and communication. Pharmaceutical manufacturing has been held to very high standards for a long time – considerably longer than food and drink, for example – and pharma packaging is held to the same high standards.
What is child-resistant packaging?
Manufacturers utilize child-resistant packaging, often known as CR packaging, to limit the danger of hazardous ingredients being consumed by children. Pharmaceutical packaging is designed to be difficult to open by children. Manufacturers, on the other hand, construct it so that most adults can access the contents of the packaging. Package testing determines whether or not persons with disabilities and the elderly can reach the packaging. Manufacturers typically use a safety cap to create child-resistant packaging. Pharmaceutical packaging is frequently required by safety regulations to incorporate such caps.
Prescription medications, over-the-counter drugs, opiates, and nicotine-containing consumables are all regularly packaged in this manner. Aside from caps and closures, child-resistant packaging includes blister packaging and even cartons.
Blister Packaging that is Child Resistant
In the pharmaceutical sector, blister packing is one of the most widely utilized packaging options. They are inexpensive, have a small packaging footprint, and provide excellent environmental protection. Blister packaging has little possibility of being thrown away accidentally at the retail level. When child-resistant packaging first hit the market in the 1970s, it only came in one shape. A bottle or jar with a safety cap was available. Blister packaging quickly surpassed them since it is not only simple to make, but it can also be made to be child-resistant.
Manufacturers utilize a multi-layer backing in the case of child-resistant blister packing. Manufacturers also utilize PVC, PVdC, PE, PP, Aclar films, and Coliform foils in addition to aluminum. This makes it more difficult for children to open the package. Adults, on the other hand, can open such packaging by peeling the back, pushing the tablet or capsule through the backing, or doing both peelings and pushing through.
The blister packing is now integrated with the external carton in newer packaging technologies. The blister is linked to the re-closable flap of the carton so that the user can easily slide out the strip. The flap's locking mechanism prevents youngsters from gaining access to the blister package. More branding area is available on the external paperboard carton. You may learn more about the different forms of blister packaging by reading about them in-depth.
Sustainability
Unlike typical consumer packaging, which protects and educates, pharmaceutical packaging goes above and beyond. Yes, it safeguards, but to a far higher extent. Yes, it informs, but it's the way it communicates that's significant. A misstated quantity can render a drug ineffective at best and fatal at worst. In many circumstances, medicine packaging must be child-resistant while also being simple to open and utilize for its intended consumers — frequently older folks. Despite the criticism, the industry adopts a rational and balanced approach to sustainability and packaging fundamental standards.
Innovating in design
Every year, the design of child-resistant main and secondary packaging improves, with innovations reaching the general market. Ziplock bags are a recent prominent improvement in packaging design. With the current growth in demand for cannabidiol (CBD) products, this alternative packaging type provides a lightweight and compact manner of protecting medicine.
Child Resistant Sprays
Nasal sprays make up the majority of aerosol sprays used in the pharmaceutical industry. With the help of CR closures, making child-resistant and senior-friendly sprays is a breeze. The spray head is usually hidden by an extra cover on most nasal sprays. The spray head is covered with child-resistant caps by the manufacturers. A common squeeze and turn mechanism can be used on the lid.
CR over-caps with a bottom lift is used in a new mechanism. The customers in this example open the cap, turn it upside down, and push it through the bottom, where it snaps into place. With the pump, the actual aerosol container is raised. The entire bottle is contained within the plastic sleeve, with the pump visible only when the customer lifts it from the bottom.
Caps and Closures
For a long time, manufacturers have used child-resistant caps and closures. Aside from the typical turn to open or close function, most of these caps have a locking mechanism. Turn and raise, Push and turn, and Squeeze and turn are the three most common mechanisms.
These caps have a locking mechanism that prevents the threads of the cap and the jar from aligning unless the locking mechanism is disengaged. They can accomplish this by exerting additional effort on the cap, such as pressing it from the top or squeezing it from the sides. To unlock the cap, the user may need to exert some more force, depending on the design.
Child Resistant Sliders
Presto Products Company has invented a child-resistant slider that allows child-resistant pouches to be manufactured. It's a slider-sealed resealable pouch. The PTE (Press-To-Engage) mechanism is included with the slider. When the user presses down on the slider tab, it will align with the ridges. Although this is difficult for five-year-olds to use, most adults, including those with disabilities, can do it with ease.
Locked4Kids
Locked4Kids is a unique carton design that combines a resealable carton with a plastic tray. The drug is kept in a plastic tray. It could be blister packs, syringes, gelatine-coated capsules, or any other type of medicine. The plastic tray has hooks on the inside that secure it to the cardboard box. A tear-resistant plastic film lining is included in the package. To unhook the plastic tray, just push the carton inwards at two diagonally positioned push points. This opens the plastic tray, allowing it to be entirely removed.
Major Market Highlights:
- On the product side of the firm, a lot of the innovation has been centered on materials. Amcor, for example, has switched from PVC to a PE thermoform blister and lidding film in its AmSky tablet and capsule blister pack. This is the world's first recyclable PE-based thermoform tablet and capsule blister pack, according to the manufacturer. When compared to other packaging options on the market today, Amcor's new, sustainable blister pack reduces its carbon footprint by 70%.
- Constantia Flexibles, a global packaging company, is also promoting products created from sustainable materials. Perpetua, the company's first recyclable polymeric mono-material, is a more environmentally friendly high-barrier packaging choice for pharmaceutical items.
- Gerresheimer, a German packaging producer, has likewise committed to becoming more sustainable, with its product family now according to the company's EcoLine criteria. Gerresheimer's well-known plastic container series for solid and liquid pharmaceuticals, including Duma, Triveni, and dropper bottles - as well as PET bottles - are developed and produced according to these criteria.
- Phillips-Medisize, a Molex business, has introduced the Aria Smart Autoinjector platform to enable innovation, distinction, and sustainability in the digital medication delivery device industry.
Conclusion: What does the future hold for Child-Resistant Packaging
Child-resistant packaging is continually improving. Despite the lack of strong child-resistant packaging rules, packaging innovations are attempting to avoid unintended poisoning in youngsters while also allowing the elderly to get their medications. One of the most difficult aspects of child-resistant packaging design is that it must be simple for the elderly yet difficult for children. Adults frequently decant their drugs into hazardous containers for easy access. Most modern child-resistant packaging strives to handle this issue as much as possible, however child-resistant packaging cannot exist without compromising some convenience.