Battery Material- Current Trend, Drivers, and Opportunities
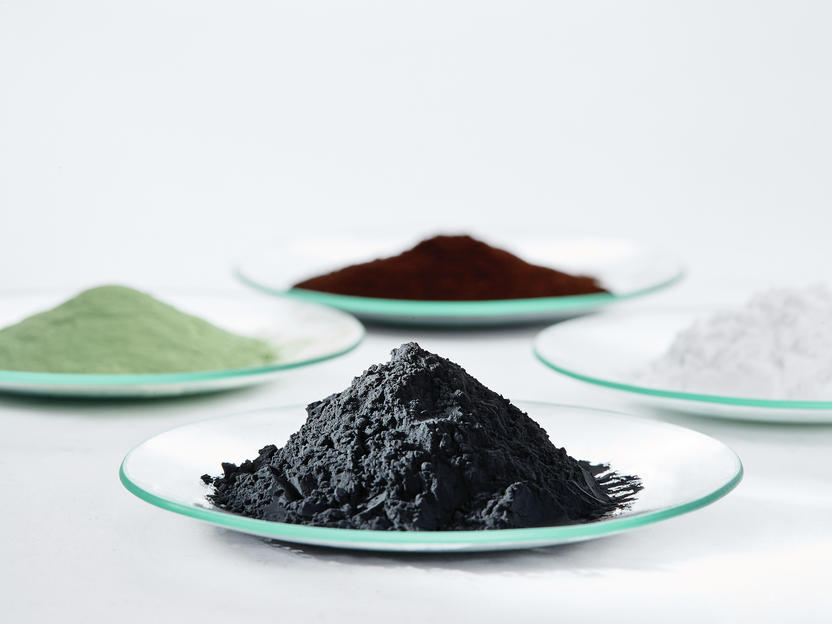
To combat climate change, the world is moving toward electric automobiles. We estimate future demand for key battery materials, taking into account possible electric car fleet and battery chemistry improvements, as well as electric vehicle battery reuse and recycling. The growth of the electric vehicle fleet and the battery capacity requirements per vehicle are important considerations. The demand for cobalt and nickel would be significantly reduced if alternate battery chemistries, such as lithium iron phosphate or innovative lithium-sulfur or lithium-air batteries, were widely adopted. Closed-loop recycling will play a tiny but growing role in lowering raw material consumption until 2050, although breakthroughs in recycling will be required to recover battery-grade materials from end-of-life batteries affordably. The usage of electric vehicle batteries for a second time extends the time it takes to recycle them.
Electric Vehicle Market
When compared to internal combustion engine vehicles, electric vehicles (EVs) have a lower environmental impact. This advantage, combined with technology advancements and government incentives, resulted in a tremendous growth in EV demand. From a few thousand vehicles a decade ago to 7.5 million in 2019, the worldwide fleet of light-duty EVs has grown dramatically. EV market penetration is still only approximately 1.5 percent globally in 2019, and future growth is likely to outstrip previous growth in absolute numbers. Concerns over the long-term supply of battery materials have been expressed as a result of the EV market's rapid growth. These include supply concerns linked with large geopolitical cobalt concentrations, social and environmental problems connected with mining, and the availability of cobalt and lithium reserves, as well as the need for quick upscaling of supply chains to meet predicted demand.
Understanding the size of future demand for EV battery raw materials is critical for guiding strategic policy and industry decisions, as well as assessing potential supply concerns and social and environmental consequences. Several studies have estimated future EV battery material demand for specific world areas, such as Europe, the United States, and China, or for individual battery materials specifically.
Current Trends in The Industry
More power is needed in the world, particularly in a clean and renewable form. Lithium-ion batteries, which are at the cutting edge of energy storage technology, are already shaping our strategy, but what can we expect in the years ahead? A battery is a collection of one or more cells, each of which contains a cathode (positive electrode), anode (negative electrode), separator, and electrolyte. The qualities of the battery are affected by the chemicals and materials used for these, such as the amount of energy it can store and output, the amount of power it can supply, and the number of times it can be drained and recharged. Battery manufacturers are continually experimenting with new chemistries in order to develop cheaper, denser, lighter, and more powerful batteries.
NEW GENERATION LITHIUM-ION BATTERIES
The flow of lithium ions from the positive to the negative electrode back and forth via the electrolyte provides energy storage and release in lithium-ion (li-ion) batteries. The positive electrode serves as the initial lithium source, whereas the negative electrode serves as the lithium host in this technique. Li-ion batteries are a collection of chemistries that are the result of decades of careful selection and optimization of positive and negative active materials. The most typical materials utilized as present positive materials are lithiated metal oxides or phosphates. Negative materials include graphite, graphite/silicon, and lithiated titanium oxides.
Li-ion technology is predicted to reach an energy limit in the next few years, based on current materials and cell designs. Nonetheless, recent discoveries of new families of disruptive active materials may be able to break through current barriers. These novel compounds can store more lithium in both positive and negative electrodes, allowing for the first time energy and power to be combined. Furthermore, the scarcity and criticality of raw materials are taken into account with these novel molecules. Before the first generation of solid state batteries, a new generation of enhanced li-ion batteries is scheduled to be deployed. They'll be perfect for applications such as renewable energy storage systems and transportation (marine, trains, and aviation) where high energy, high power, and safety are required.
LITHIUM-SULFUR BATTERIES
Lithium ions are kept in active materials in lithium-ion batteries, which act as stable host structures during charge and discharge. There are no host structures in lithium-sulfur (Li-S) batteries. The lithium anode is consumed during discharging, and sulfur is converted into a variety of chemical compounds; when charging, the process is reversed. Major technological obstacles have already been overcome, and the maturity level is rapidly approaching full-scale prototypes. This technology is predicted to hit the market shortly after solid state lithium-ion for applications that require a lengthy battery life.
SOLID STATE BATTERIES
In terms of technology, solid state batteries constitute a paradigm change. Ions flow from one electrode to another across the liquid electrolyte in modern lithium-ion batteries (also called ionic conductivity). The liquid electrolyte is replaced by a solid component in all-solid-state batteries, but lithium ions can still travel through it. This notion is not new, but during the last ten years, new families of solid electrolytes with extremely high ionic conductivity, akin to liquid electrolytes, have been developed, allowing this technological barrier to be overcome. As technology advances, a variety of all-solid-state batteries are likely to hit the market. Lighter solid-state battery solutions with a metallic lithium anode should be commercially available in the near future.
Recycling scenarios
EoL battery recycling provides a secondary supply of materials. We study the implications of recycling efficiencies of three recycling scenarios on primary material demand, including recovered quantities and some discussion of recycled material characteristics, assuming 100% collection rates. The "without recycling" scenario captures the principal material consumption when EoL batteries are not collected and recycled. Pyrometallurgical (pyro) and hydrometallurgical (hydro) recycling are two currently commercialized recycling methods. For cathode-to-cathode recycling, direct recycling is being developed. Pyro, hydro, and direct recycling are assumed in the three recycling scenarios for NCX and LFP batteries, respectively, whereas mechanical recycling is assumed in all three situations for Li-S and Li-Air batteries.
- The lithium in the slag can be processed to make battery-grade lithium compounds, but this is only cost-effective when the price of lithium is high and recycling is done in large quantities.
- Shredding disassembled modules and/or cells is the first step in the hydrometallurgical recycling process. The components are subsequently separated into cathode powder, anode powder, and mixed aluminum and copper scraps using a series of physical separation procedures. The mixed aluminum and copper scraps may be further divided into aluminum scraps and copper scraps depending on scrap metal pricing.
- Except for cathode powder recycling, the direct recycling scenario is identical to the hydro scenario. The cathode powder is collected and then regenerated in the direct method by reacting with a lithium source (relithiation and upgrading). As a result, lithium, nickel, cobalt, and manganese are all recovered as a single battery-grade material. Because no lithium refining is required, as is the case with pyro and hydro, lithium recovery in the direct approach is cost-effective, at least on a lab-scale level.
Future Trends Analysis
The future market share of BEVs and PHEVs, as well as the capacity of EV batteries, are also important factors in estimating the quantity of materials required. While many factors influence battery capacity, including EV range, fuel economy, and powertrain configurations, we conducted a sensitivity analysis on two extreme scenarios: 100 percent BEV with 110 kWh capacity (large SUVs such as the Tesla Model S Long Range Plus) and 100 percent PHEV with 10 kWh capacity, to see where future material demand might be limited.
Existing methods should be refined in the near future, with simple modifications that can have a major influence on battery costs and energy density. Looking farther forward, new technologies such as Solid State Batteries, which have been under development for some time, are expected. We should also see new chemistries emerge, such as sodium ion batteries, which are being investigated by a number of prominent manufacturers.
This industry is attracting a lot of resources and investment. This has ramifications not only for batteries, but also for businesses related to batteries, such as new mining technologies, battery cycling innovation, integration, charging infrastructure, and vehicle-to-grid applications.