Composite Materials: Growing Application for Lightweight Products
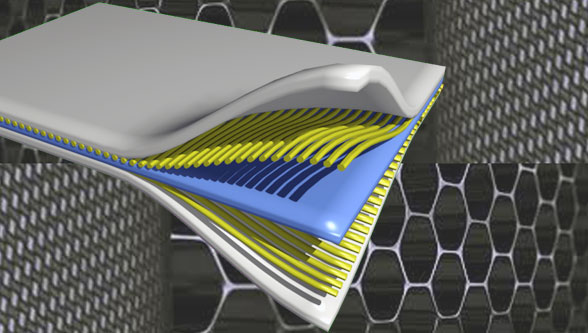
“From housing early civilizations to facilitating future inventions, composite materials have played an important role in human history. Corrosion resistance, design flexibility, longevity, light weight, and strength are only a few of the advantages of composites. Composites are used in a wide range of applications, including construction, medical applications, oil and gas, transportation, sports, aerospace, and many others. Without composite materials, certain applications, such as rocket ships, will most likely never get off the ground.”
Composites can be found in nature. Long cellulose fibres are kept together by a material called lignin in a piece of wood, making it a composite. Composite materials are created by combining two or more materials with distinct properties that do not dissolve or mix together. The composite's various materials work together to give it its distinct properties. For thousands of years, humans have used composite materials in a variety of applications. Early Egyptians and Mesopotamian settlers used a mixture of mud and straw to construct solid and stable structures around 1500 BC.
The fibre-reinforced polymers (FRP) industry arose from the growth and demand for composite materials. By 1945, over 7 million pounds of glass fibres had been used in a variety of items, often for military purposes. After the war, composite materials exploded in popularity, growing at a breakneck pace through the 1950s. Composite pioneers were attempting to break into new industries such as aerospace, manufacturing, and transportation. The benefits of FRP composites, especially their corrosion resistance, were quickly recognised by the public sector. One clear commodity that gained was boats. In 1946, the first composite commercial boat hull was published. In 1947, a complete composite car body was built and tested. The 1953 Chevrolet Corvette was born as a result of this.
The invention of the car ushered in a slew of modern moulding techniques, including compression moulding of bulk moulding compound (BMC) and sheet moulding compound (SMC) (SMC). For the automotive industry and other sectors, the two techniques have emerged as the prevailing form of moulding. Manufacturing techniques such as large-scale filament winding, pultrusion, and vacuum bag moulding were introduced in the early 1950s. The marine industry became the largest user of composite materials in the 1960s. The first carbon fibre was patented in 1961 and became commercially available some years later.
The composites industry is still developing today, with much of the expansion focused on renewable energy. Engineers can design to customise the composite based on the performant requirements, for example, making the composite sheet very strong in one direction by aligning the fibres that way, but weaker in another direction where strength is less necessary. Engineers may also choose properties including heat resistance, chemical resistance, and weathering resistance by selecting the right matrix content.
Natural fibres are being used as reinforcements in composites to replace synthetic fibres due to an increase in environmental consciousness and recognition of the need for sustainable growth in recent years.
Composite materials market split by applications
A laminar structure is the most common form of fibre-reinforced polymer, which is created by stacking and bonding thin layers of fibre and polymer until the desired thickness is achieved. A defined degree of anisotropy in composite properties can be achieved by changing the fibre orientation among layers in laminate structures.
Corrosion resistance, light weight, strength, lower production costs, increased efficiency, design flexibility, and longevity are only a few of the advantages of composites. As a result, composite materials are used in a wide variety of industries, and some of their most popular applications are mentioned below.
Aerospace
The promise of composite materials for large-scale applications in aviation has been demonstrated by major original equipment manufacturers (OEMs) such as Airbus and Boeing. NASA is still on the lookout for new ideas and space applications for rockets and other spacecraft from composite manufacturers. In industrial, civilian, and military aerospace applications, thermoset composites are being specified for bulkheads, fuselages, wings, and other applications.
Composites are also used in air-foil surfaces, antenna structures, compressor blades, engine bay doors, fan blades, flywheels, helicopter transmission structures, jet engines, radar, rocket engines, solar reflectors, satellite structures, turbine blades, turbine shafts, rotor shafts in helicopters, wing box structures, and other areas.
Business/Appliance
Composite materials have more design and manufacturing versatility than metal alloys, so they can be used as an alternative to metal alloys in appliances. Unlike most other sectors, the appliance industry moves at a rapid pace. Furthermore, design and function are affected by both technological advances and shifting customer preferences. Appliance and business equipment, such as equipment panels, bases, handles, and trims in appliances, power tools, and a variety of other applications, use composite materials. In the appliance industry, composites are used in dishwashers, dryers, freezers, ovens, ranges, refrigerators, and washers.
Consoles, control panels, handles, kick plates, knobs, engine housings, shelf brackets, side trims, vent trims, and many other parts in the equipment used composites.
Architecture
Composite materials are becoming the material of choice for architectural applications due to their aesthetic qualities, functionality, and durability. Composite materials enable architects to construct designs that would be difficult or impractical with conventional materials, as well as increase the thermal performance and energy efficiency of building materials and meet building code requirements. Composite materials are also versatile in terms of construction and can be moulded into complex shapes. They come in a number of thicknesses and can be corrugated, curved, ribbed, or contoured in a variety of ways.
Furthermore, using composite materials, a conventional look such as copper, chrome, or gold, marble, and stone can be achieved at a fraction of the cost. As a result, the architectural community is seeing significant progress in terms of understanding and application of composites in commercial and residential construction.
Transportation and Automobiles
Composites aren't new to the automotive industry. One of the largest markets for composite materials is in this country. The most significant benefit of using composite materials is weight loss. Since it takes less fuel to drive a lighter car or truck forward, it is more fuel efficient. Composites help make cars lighter and more fuel efficient, in addition to allowing ground-breaking vehicle designs. Bearing components, bodies, connecting rods, crankshafts, cylinders, motors, pistons, and other composite materials are used.
Though carbon fiber-reinforced polymers (CFRP) in automobiles receive the most coverage, composites also play an important role in improving fuel efficiency in trucks and transportation systems. Composite is now being used by a number of state transportation departments in the United States to strengthen the bridges that these trucks drive on.
Infrastructure and construction
Construction is one of the most important markets for composites around the world. Composites with extremely high strength and ideal construction materials can be made. Many conventional materials for home and office architectural products, such as doors, fixtures, moulding, roofing, shower stalls, swimming pools, vanity sinks, wall panels, and window frames, are being replaced by thermoset composites. From buildings and bridges to highways, railways, and pilings, composites are used all over the world to assist in the construction and maintenance of a wide range of infrastructure applications.
Corrosives
Composite-materials-based products are resistant to harsh chemical and temperature environments for a long time. Chemical handling applications, corrosive conditions, outdoor exposure, and other harsh environments such as chemical manufacturing plants, oil and gas refineries, pulp and paper converting, and water treatment facilities also use composites. Cabinets, ducts, fans, grating, hoods, pumps, and tanks are all popular applications. Fibre-reinforced polymer composite pipes are used for a variety of uses, including sewer repairs and drainage projects, as well as desalination, oil, and gas. Fibre-reinforced polymer is a remedy when corrosion occurs in pipes made of conventional materials.
Energy
From the early days of glass fibres as major reinforcements for composite materials, material processing has progressed to carbon fibres, which are lighter and stronger. The energy industry is being reshaped by advances in composites, especially those from the US Department of Energy. Composites aid in the use of wind and solar energy, as well as the productivity of conventional energy providers. Composite materials provide wind turbine producers with strength and processing flexibility, as well as lightweight parts and products. Over the last few years, the wind industry has set new milestones for installation.
The Global Wind Energy Council predicts that global wind capacity will double in the next few years, continuing the industry's upward trend. Wind turbine blades, for example, rely heavily on composites for their construction.
Major Market Highlights
- Solvay and Leonardo announced a composite research collaboration in February 2021, announcing the opening of a new lab for the development of composite materials and manufacturing processes for the aerospace industry.
- Solvay and Strata opened a new manufacturing facility in Al Ain, UAE, in June 2020. This manufacturing facility was created specifically for aerospace-grade pre-impregnated carbon fibres, and it is the first in the Middle East and Africa region, as well as the fourth in the world.
- Scott Bader's Australia business unit purchased Summit Composites Pty Ltds. entire assets in June 2020. This purchase helped the company expand its market share in the Pacific region.
Effect of COVID-19 on the Global Composites Market
Our team has noticed that demand for composites is slowing down during the pandemic era. However, it is expected to rise at a healthy pace starting in mid-2021. Many countries around the world have imposed stringent lockout regulations to prevent the pandemic from spreading, causing all sorts of business practises to be hampered.
The closure of the marketplace has completely disrupted the demand and supply of raw materials, as well as product manufacturing and distribution. Transportation, aircraft, oil and gas, and computer sectors have also suffered significant financial losses. This has resulted in low demand for a variety of products and materials, including composites.
Moving Forward
Composites have many benefits, including the ability to use a wide variety of material combinations, allowing for design flexibility. In addition, the composites can be conveniently moulded into complex shapes. Materials may be custom tailored to meet particular requirements. Composites are lighter in weight than most woods and metals, and they have a lower density than certain metals. They are more durable than other materials. Climate and harsh chemicals have no impact on the products. Composites have a long life expectancy and need minimal upkeep.
The design possibilities for composite products are numerous due to the large range of available reinforcement, matrix, and their shapes, manufacturing processes, and each resulting in their own distinct composite products. As a result, a composite and its manufacturing process can be selected to better fit the emerging rural communities in which the goods will be manufactured and used. The study of composite materials is still ongoing. Nanomaterials—materials with incredibly small molecular structures—and bio-based polymers are two fields of concern. Several factors must be considered in order to maximise the benefits of composites: a) concept creation, b) material selection and formulation, c) material design, d) product production, e) industry, and f) regulations.