The Future of Semiconductor Industry: Exploring the Benefits of IoT Applications
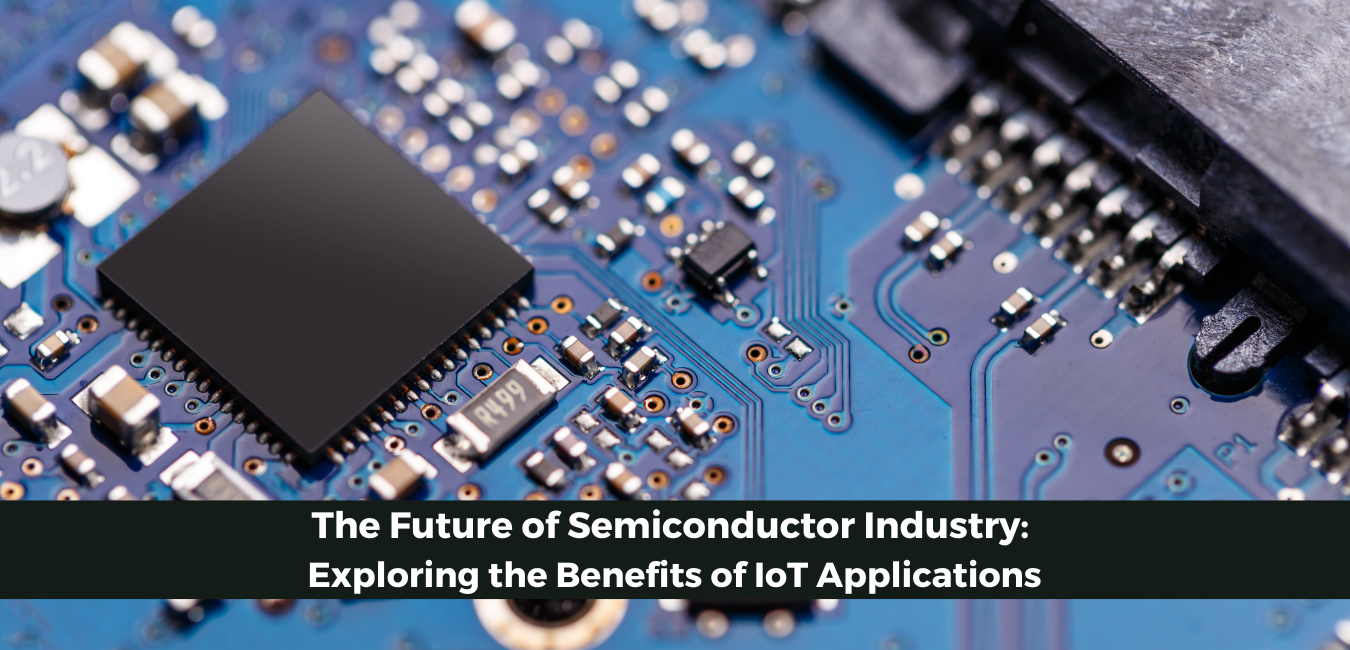
The semiconductor industry is undergoing a massive transformation with the introduction of the Internet of Things (IoT). With this new technology, more and more devices are being connected to each other and they are able to communicate with each other without any manual intervention.
Industry leaders believe that the IoT market will surpass $1 trillion by 2024 with a CAGR of 13%. A survey found that IoT has had a better growth in areas like enterprise, home automation, and retail analytics and solutions. It is now driving the growth of micro controllers, sensors, chips, which will eventually benefit the semiconductor industry. With the processing, sensing, and communications significantly growing massively, the market will evolve and grow in an unprecedented way over a period of time.
Like you already saw that the potential for this technology is immense and its applications can be used in almost every sector. By utilizing IoT applications, the semiconductor industry can benefit from improved data collection, better communication, and increased efficiency. This will make it easier for companies to monitor their products and services better, leading to improved customer satisfaction.
It will also help reduce costs associated with production which could result in lower prices for consumers. In short, by taking advantage of IoT applications in the future, the semiconductor industry has an opportunity to become even more successful than it already is.
Exploring the Possibilities of IoT Applications in Semiconductors
The Internet of Things (IoT) has been rapidly growing in recent years, and it's no surprise that the semiconductor industry has been quick to adopt the technology. IoT applications in the semiconductor industry can be broken down into a few key areas: manufacturing, logistics, and equipment monitoring.
Manufacturing: IoT technology can be used to monitor and control the production process in semiconductor manufacturing. This includes monitoring temperature, humidity, and other environmental conditions to ensure that the manufacturing process is running smoothly and producing high-quality semiconductors. Additionally, IoT sensors can be used to monitor the production equipment and alert maintenance personnel when repairs or maintenance is needed.
Logistics: IoT technology can be used to track and monitor semiconductor shipments as they move through the supply chain. This includes monitoring the temperature, humidity, and other environmental conditions of the shipments to ensure that the semiconductors are not damaged during transport. Additionally, IoT technology can be used to track the location of shipments and alert logistics personnel when a shipment is delayed or has been lost.
Equipment monitoring: IoT sensors can be used to monitor the performance of the equipment used in the semiconductor industry. This includes monitoring the temperature, humidity, and other environmental conditions of the equipment to ensure that it is operating properly. Additionally, IoT sensors can be used to monitor the performance of the equipment and alert maintenance personnel when repairs or maintenance is needed.
Overall, IoT technology has the potential to greatly improve the efficiency and effectiveness of the semiconductor industry by providing real-time monitoring and control of the production process, logistics, and equipment. This ultimately leads to better quality of products and cost savings for the industry.
How to Leverage Connected Systems and Automation Through IoT?
The Internet of Things (IoT) allows for the connection and automation of various systems and devices through the use of sensors, actuators, and communication technologies. To leverage connected systems and automation through IoT, one can take the following steps:
- Identify the systems and devices that need to be connected and automated.
- Determine the communication protocols and technologies that will be used to connect the devices and systems.
- Implement sensors and actuators on the devices and systems to enable data collection and control.
- Use software and platforms to integrate the connected devices and systems, and to manage the data collected by the sensors.
- Create rules and logic to automate processes and actions based on the data collected by the sensors.
- Continuously monitor and optimize the performance of the connected systems and automation to improve efficiency and effectiveness.
- Ensure the security of the connected systems and automation as well as the data transmitted.
By following these steps, one can effectively leverage connected systems and automation through IoT to improve efficiency, increase productivity, and gain valuable insights from the data collected.
The Impact of IoT on Automation and Cost Reduction in Semiconductors
The Internet of Things (IoT) has had a significant impact on automation and cost reduction in the semiconductor industry. IoT devices, such as sensors and actuators, can be integrated into semiconductor manufacturing processes to improve efficiency and reduce costs. Automation of processes such as data collection, analysis, and decision-making can lead to increased productivity, improved product quality, and reduced human error. Additionally, IoT-enabled equipment can be remotely monitored and controlled, reducing the need for manual intervention and maintenance. Furthermore, IoT devices can also be used to collect data and analyze it to optimize production processes, lower energy consumption, and improve supply chain efficiency.
Benefits of Using IoT in Semiconductors for Predictive Maintenance
The use of Internet of Things (IoT) in semiconductor manufacturing can bring several benefits when it comes to predictive maintenance. Some of these benefits include:
- Real-time monitoring: IoT sensors and devices can be used to collect data on the performance and condition of equipment and machinery in real-time, which allows for early detection of potential issues and proactive maintenance.
- Increased efficiency: By using predictive maintenance, semiconductor manufacturers can schedule maintenance and repairs at the most optimal time, reducing downtime and increasing overall efficiency.
- Cost savings: Predictive maintenance can help reduce the need for emergency repairs and prolong the life of equipment, ultimately resulting in cost savings for the manufacturer.
- Improved safety: By identifying potential issues before they become critical, predictive maintenance can help improve safety for employees by reducing the risk of equipment failure.
- Predictive analysis: With the help of machine learning, IoT sensors data can be analyzed to predict future failures, enabling the manufacturer to take preventative measures.
- Better decision making: With the real-time data from IoT sensors, manufacturers can make more informed decisions about equipment and production processes, improving overall performance and efficiency.
- Remote monitoring: IoT devices can be connected to remote servers, allowing for monitoring of equipment from remote locations, which can be especially useful for large manufacturing facilities.
To conclude
Overall, the use of IoT in semiconductor manufacturing can bring significant benefits when it comes to predictive maintenance, improving efficiency, safety, and cost savings while enabling better decision making.